[stextbox id=”alert” defcaption=”true”]Don’t use microstepping to increase the “precision” of your machine.[/stextbox]
The HobbyCNC driver boards allow five different modes of driving your stepper motors. These can be set differently between each axis if desired. As a side note, 1/8 and 1/16 stepping MAY require quite a lot of computer process power!
We recommend using 1/2 or 1/4 step. This produces almost full power and usually avoids any resonance issues. The finer the micro step the less power you’ll have.
The Microstepping is set as follows. Note: The right-most jumper is for Idle Current Reduction and is on the PRO boards only.
J1 | J2 | J3 | ||
---|---|---|---|---|
1/1 Step | ON | ON | OFF | ![]() |
1/2 Step | ON | OFF | OFF | ![]() |
1/4 Step | OFF | ON | ON | ![]() |
1/8 Step | OFF | ON | OFF | ![]() |
1/16 Step | OFF | OFF | ON | ![]() |
In Mach3 it appears you need to multiply steps per revolution of the motor times the microstep setting to derive “Pulses Per Revolution”. (I think)
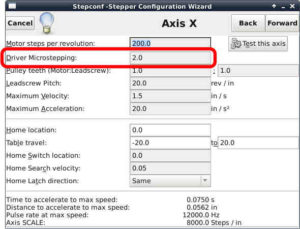
LinuxCNC Microstepping Configuration. Repeat for each axis. This is set in the StepConfig wizard.